الکتروگالوانیزاسیون
پردیس فناوری کیش-طرح مشاوره متخصص صنعت ومدیریت-گروه مهندسی مواد
الکتروگالوانیزاسیون فرایندی است که در آن یک لایه فلز روی به سطح فولاد متصل میشود تا از خوردگی آن محافظت کند. این فرایند جز فرایندهای آبکاری محسوب میشود، استفاده از یک جریان الکتریسیته در یک محلول نمکی روی با آند روی و کاتد فولادی منجر به این فرایند میشود. آبکاری روی دارای موقعیت غالب در میان سایر گزینههای فرایند آبکاری الکتریکی، بر اساس تناژ آبکاری در سال است. پرکاربردترین فولاد نورد سرد گالوانبزه، فولاد SECC است. در مقایسه با گالوانیزه گرم آبکاری روی با مزایای قابل توجهی ارائه میشود:
- رسوب با ضخامت کم برای دستیابی به عملکرد مشابه
- در دسترس بودن پوشش بیشتر برای افزایش کارایی و رنگ
- رسوب روشنتر و زیباتر
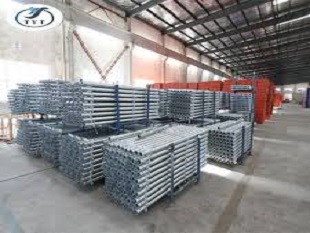
فرایند الکتروگالوانیزاسیون
حفاظت در برابر خوردگی که توسط لایه الکترودی از روی ایجاد میشود، عمدتاً به دلیل اختلاف پتانسیل الکترودی روی در برابر آهن (و یا سطح زیرلایه) است. روی به عنوان محافظ از آهن (فولاد) عمل میکند. در حالی که پتانسیل کاهشی فولاد نزدیک به E SCE = -400 mV است (پتانسیل مربوط به جدول استاندارد پتانسیل کاهشی (SCE)است)، بسته به ترکیب آلیاژ، پتانسیل کاهشی روی در حدود E SCE = -980 mV است. در این فرایند فولاد تحت حفاظت کاتدی قرار میگیرد. پوششهای تبدیلی (کروم شش ظرفیتی (CrVI) یا کروم سه ظرفیتی (CrIII) بسته به نیاز OEM) برای افزایش شدید محافظت از خوردگی با ایجاد یک لایه مهارکننده ای از کروم و هیدروکسید روی استفاده میشوند. بازه ضخامت این فیلمهای اکسیدی از 10nm برای باریکترین تا ۴μm برای ضخیمترین کروماتهای سیاه میباشد.
علاوه بر این، پوشش روی ممکن است توسط یک پوشش فوقانی برای افزایش مقاومت خوردگی و عملکرد اصطکاک تقویت شود.
الکترولیتهای سیانیدی
این الکترولیتها حاوی سولفات سدیم و هیدروکسید سدیم (NaOH) هستند. همه آنها از عوامل روشنکننده اختصاصی استفاده میکنند. روی به عنوان یک ترکیب سیانیدی Na2Zn(CN)4 و همچنین یک ترکیب زینکاته Na2Zn([[[:en:Hydroxide|OH]]])4 محلول است. کنترل کیفیت این الکترولیتها نیاز به تجزیه و تحلیل منظم Zn, NaOH و NaCN دارد. NaCN: روی میتواند بین سطح ۲ تا ۳، بسته به درجه حرارت حمام و میزان روشنایی مورد انتظار باشد.
الکترولیتهای قلیایی غیر سیانیدی
این الکترولیتها حاوی هیدروکسید روی و سدیم است. در اکثر آنها عوامل افزودنی اختصاصی روشنکننده سطح مشابه با حمامهای سیانید استفاده میشوند. اضافه کردن افزودنیهای آمینی، به بهبود توزیع فلز بین مناطق با شدت جریان بالا و پایین کمک میکند. با توجه به کارایی مورد نظر، آبکار میتواند بیشترین میزان روی را برای افزایش بهرهوری یا کمترین میزان روی برای انتقال قدرت بهتر (در مناطق تراکم جریان پایین) انتخاب کند. برای توزیع ایدهآل فلز، غلظت فلز روی بین 6-14 g/L و سدیم هیدروکسید در 120 g/L باید باشد. اما برای بالاترین بهرهوری، غلظت فلز روی بین 14-25 g/L و سدیم هیدروکسید120 g/L باید باشد. فرایندهای قلیایی غیر سیانیدی میتواند شامل غلظتهای کم یا زیاد از روی باشند، غلظتهای زیاد میتوانند توزیع یکنواخت بهتری مستقل از کم یا زیاد بودن شدت جریان در مقایسه با محلولهای اسیدی بدهند.
الکترولیتهای با سرعت بالا
توجه به سرعت بالا در کاربردهایی که در آن کوتاهترین زمان آبکاری بحرانی است هایز اهمیت میباشد (به عنوان مثال کویل فولادی). حمام حاوی سولفات روی و کلرید تا حداکثر میزان حلالیت است. اسید بوریک ممکن است به عنوان یک بافر pH یا برای کاهش اثر سوختگی در تراکمهای جاری بالا استفاده شود. این حمامها حاوی تعداد کمی از یکنواخت کنندههای دانه میباشند. اگر یک مورد استفاده شود، ممکن است سدیم ساخارین باشد.
الکترولیتهای سنتی
این الکترولیتهای بر اساس آمونیوم کلرید، گزینههای امروز شامل آمونیم، پتاسیم یا الکترولیتهای آمونیوم پتاسیم مخلوط میشوند. غلظت روی بالا باعث افزایش کارایی حمام میشود (سرعت آبکاری)، در حالی که سطوح پایینتر غلظت توانایی حمام را برای استفاده با شدت جریان پایین بهبود میبخشد. بهطور معمول، غلظت فلز روی بین ۲۰ تا ۵۰ گرم در لیتر (۲٫۷–۶٫۷ اونس / گال) متغیر است. pH بین ۴٫۸ و ۵٫۸ متغیر است.