تنش در خاک
پردیس فناوری کیش- طرح مشاوره متخصصین صنعت و مدیریت-گروه مکانیک
مکانیک خاک soil mechanic
مکانیک خاک شاخهای از مهندسی است که به توضیح رفتار خاک میپردازد.
علم مکانیک خاک متفاوت ازمکانیک سیالات و مکانیک جامدات و است به این دلیل که خاک محیطی است ناهمگون و متشکل از سیالات (معمولاًهوا و آب) و ذرات گوناگون (معمولاً رس ، ماسه یا شن)یا گاهی مواد آلی ، مایعات، گازها .
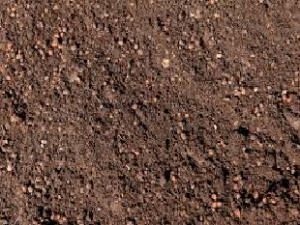
توزیع تنش در خاک
تأثیر فشار ناشی از فونداسیون، خاک زیر آن در اعمـاق مختلـف، تحـت افـزایش تـنش قـرار مـیگیـرد. افزایش خالص در تنش خاک، بستگی به بار وارد بر واحد سطح تماس شالوده، عمـق و فاصـله نقطـه مـورد مطالعه از شالوده و چند عامل دیگر دارد.
با تأثیر سربار، تنشهای فشاری در لایههای خاک به وجود آمـده و باعث فشرده شدن آن میشود.
فشردگی خاک ناشی از تغییر شکل فشاری و جابجـایی ذرات خـاک، رانـده شدن هوا و آب از حفرات خاک و عوامل دیگر است.
در یک خـاک بخـصوص، یـک یـا تعـدادی از عوامل فوق ممکن است مشارکت داشته باشند. از آنجایی که فشرده شدن خاک باعث نشست سازۀ واقع بـر روی آن میشود، از نقطه نظر مهندسی به این پدیده، نشست خاک میگویند.
برای محاسـبات نشـست، لازم است افزایش خالص تنش قائم خاک به علت احداث شالوده تعیین شود. با استفاده از تئوری الاستیسیته، اصول تعیین افزایش تنش قائم در خاک مورد بررسی قرار میگیرد.
شرط های لازم برای پایداری
بارهای ناشی از یک سازه از طریق پی، به خاك منتقل میشود. در طراحـی هـر پـی دو شـرط پایداری زیر باید تامین شود.
⇐ پی نباید فرو بریزد، یا زیر هر بارگذاری قابل تصور ناپایدار شود.
⇐ نشست سازه باید در داخل محدوده مجاز باشد. اغلب نشست در طرح پیهای کم عمق تعیین کننده هستند.
اگر مقدار نشست پـس از مقـادیر حداکثری بیشتر باشد، عملکرد پی در هالهای از ابهام قرار گرفته و بـرای سـازه اصـلی خطـر جـدی محسوب میشود.
نشست خاک
نشستهای پی را باید با دقت زیادی برای ساختمانها، پلها، برجها، نیروگاهها و سازههـای پرهزینـۀ مـشابه تخمین زد. در سازههایی همچون خاکریزها، سدهای خاکی، بنـدهای خـاکی، سـپرکوبی مهاربنـدی شـده معمولاً حاشیۀ خطای بزرگتری برای نشست وجود دارد.
به جز در مواردی که به طور تصادفی پیشبینیها با واقعیت منطبق باشند، محاسبات نشست خاک را تنها میتوان به بهترین شکل از تغییر شکل قابل انتظار پس از اعمال بار تخمین زد.
در زمان نشـست حالـت تـنش فعلی جسم (یا وزن خود) خاک تحت تأثیر بار اضافی اعمال شده به حالت جدیـدی تبـدیل مـیشـود. تغییـر تنش q∆ ناشی از این بار اضافی به تجمع زمانی غلتش، لغزش، خردشدگی و تغییر شکلهای الاستیک ذرات در منطقۀ محدود نفوذ در زیر سطح بارگذاری منجر میشود. تجمع آماری ایـن حرکـات در جهـت مـورد نظر نشست نام دارد.
انواع نشست خاک
∗ نشست تحکیمی
∗ نشست آنی