انواع پمپ هیدرولیک
پردیس فناوری کیش-طرح مشاوره متخصص صنعت و مدیریت-گروه مهندسی مکانیک
پمپ رفت و برگشتی
معمولا موتورهای الکتریکی تامین کننده نیروی محرکه لازم در این مدل هستند.
در این مدل پمپ، با چرخش میل لنگ، پیستون در سیلندر جلو و عقب رفته یا اصطلاحا حرکت رفت و برگشتی می کند.
مکش ایجاد شده در سیلندر که ناشی از عقب رفتن پیستون است، باعث کشیده شدن مایع به داخل سیلندر می شود.
مایع از یک شیر ورودی به داخل سیلندر کشیده می شود.
وقتی پیستون به جلو حرکت کند، ورودی بسته شده و مایع از شیر خروجی خارج می شود.
شیرهای ورودی و خروجی یک طرفه هستند و ورود و خروج مایع را در هنگام حرکت پیستون کنترل می کنند تا
مانع جابجایی اشتباه مایع به قسمت کم فشار و بالعکس شوند.
اگرچه حجم انتقال یافته در این پمپ ها ثابت است، اما دامنه حرکت عضو رفت و برگشتی می تواند با مکانیزمی قابل تنظیم باشد. به همین دلیل این پمپ ها اولین انتخاب برای سرویس های تزریق هستند.
از معایب این پمپ ها می توان به موارد زیر اشاره کرد:
1- نبض یا Pulse (به عنوان پدیده نامطلوب در سیستم لوله کشی)
2- وابستگی به عملکرد شیر یک طرفه (Check Valve) در ورودی و خروجی
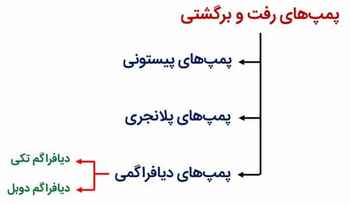
پمپ پیستونی
در پمپ های پیستونی ساختار انتقال قدرت شبیه به پمپ های پلانجری است.
با این تفاوت که در اختلاف فشار کمتری می توانند حجم مشخصی از سیال را جا به جا کنند. علت آن را می توان در ضریب رعنایی بالاتر میله پیستون آن و در نهایت کمانش راحت تر آن دانست.
محدوده کاری
این پمپ ها معمولا تا اختلاف فشار 150bar مورد استفاده قرار می گیرند.
کاربرد
- پمپ های هیدرولیکی برای ماشین آلات سنگین
- پمپ انتقال نفت خام
پمپ پلانجری
در پمپ های پلانجری، نیروی دورانی موتور از طریق میل لنگ و یک میل-پیستون که حرکت دورانی را به حرکت رفت و برگشتی تبدیل می نماید به پیستون منتقل می شود.
پمپ های پلانجری بهترین گزینه برای پمپاژ سیالات با ویسکوزیته بالا می باشند.
محدوده کاریپمپ های پلانجری
از این پمپ ها معمولا تا اختلاف فشار 2100bar می توان بهره برداری نمود.
مزایای پمپ های پلانجری
این پمپ در میان سایر انواع خانواده پمپ های جابجایی مثبت می تواند در بالاترین محدوده اختلاف فشار، سیال را جا به جا نماید.
پمپ دیافراگمی
پمپ های دیافراگمی را بر اساس تعداد دیافراگم می توان به انواع ذیل تقسیم بندی نمود:
- دیافراگم تکی(Single Diaphragm)
- دیافراگم دوتایی (Double Diaphrag)
همچنین بالاترین درجه نشت بندی را دارا بوده و به جز در ویسکوزیته دینامیکی 400cp از رایج ترین پمپ های تزریق در صنعت نفت، گاز و پتروشیمی محسوب می شوند.
در حالت دیافراگم دوتایی، فاصله میان دو دیافراگم با لایه نازکی از روغن پر شده یا آن را در فشاری نزدیک به فشار خلا قرار می دهند. یک سنسور معروف به
Rupture detector فضای موجود میان دو دیافراگم را مورد پایش قرار می دهد.
محدوده کاری
از این پمپ ها معمولا تا اختلاف فشار 250bar می توان استفاده کرد؛ که در این اختلاف فشار معمولا می توان دبی 500l/h را پمپاژ نمود.
مزایا
به دلیل قدرت نشت بندی بالا برای پمپ کردن مواد شیمیایی اشتعال پذیر و یا خطرناک مناسب هستند.
پمپ چرخشی
این پمپ ها با استفاده از مکانیسم چرخشی، سیال را جا به جا می کنند.
در واقع خلاء ایجاد شده ناشی از چرخش چرخ دنده ها، منجر به جذب و هدایت سیال می شود.
مزیت مهم این پمپ ها که آن ها را بسیار کارآمد کرده این است که
می توان از آن ها برای پمپ کردن سیالات ویسکوز (چسبناک) استفاده کرد.
در این پمپ ها با افزایش ویسکوزیته، سرعت گردش بالاتر می رود و سیال در سیستم انتقال می یابد.
ین پمپ ها که خود یکی از انواع پمپ های جابجایی مثبت هستند، در حالت کلی خود به چند دسته تقسیم می شوند که در شکل زیر قابل مشاهده است:
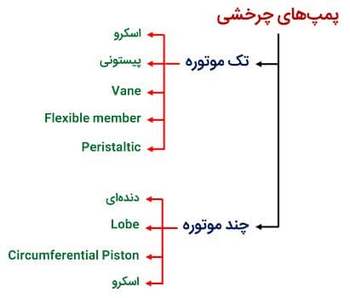
پمپ های پرکاربرد از گروه پمپ های روتوری به شرح ذیل است:
- پمپ های اسکرو
- پمپ های دنده ای (دنده داخلی و خارجی)
- پمپ های تیغه ای
- پمپ های گوشواره ای
پمپ اسکرو یا پیچ ارشمیدس
این دسته پمپ اولین و مهم ترین نماینده خانواده پمپ های چرخشی هستند.
حرکت سیال در این گونه از پمپ ها براساس تغییر زاویه یک پیچ در پوسته است.
به دلیل ابداع این پمپ توسط ارشمیدس این پمپ ها را با نام پیچ ارشمیدس (Archimedes rotary pump) نیز می شناسند.
محدوده کاری
محدوده سرعت جریان: 189 تا 56781 لیتر در دقیقه
محدوده اختلاف فشار: 310 بار
پمپ دنده ای (gear Pump)
این پمپ ها شامل دو نوع دنده ای داخلی و دنده ای خارجی می باشند.
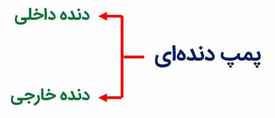
پمپ دنده ای خارجی
پمپ های دنده خارجی یکی از پمپ های محبوب هستند و اغلب به عنوان پمپ های روان کاری در ماشین آلات، در واحد انتقال قدرت مایع و به عنوان پمپ های روغن در موتور استفاده می شود
محدوده کاری
پمپ های کوچک دنده خارجی معمولا در دور 1750Rpm یا 3450Rpm عمل می کنند و مدل های بزرگتر با سرعت تا 640 دور در دقیقه عمل می کنند. این پمپ ها بهتر است سیال را حداکثر در اختلاف فشار 120 بار جاه به جا نماید.
پمپ دنده ای داخلی
پمپ های دنده داخلی فوق العاده همه کاره هستند و می توان از آن ها در محدوده وسیع ویسکوزیته ای و دمایی استفاده کرد.
این به دلیل نقطه ی تکین لقی (clearance) (فاصله ی بین انتهای دنده دنده روتور و سر پمپ) است.
این لقی (clearance) قابل تنظیم است تا بتواند خود را به درجه حرارت بالا، حداکثر بهره وری در مایعات ویسکوزیته بالا تطبیق دهد.