صنعت تولید آهن و فولاد در جهان با سابقه تاریخی بیش از ۵۰۰۰ سال در عصر کنونی و به علت نیاز فراوان به آن در زمینه فعالیتهای صنعتی و ساختمانی به عنوان یک صنعت جامع و زیربنائی مورد توجه می باشد. در فرایند احیا مستقیم ، با استفاده از عوامل احیا کننده در دمای پایین تر از دمای نقطه ذوب اکسیژن سنگ آهن حذف می شود. کربن جامد تنها نقش کوچکی در فرایند احیا مستقیم سنگ آهن بازی می کند.
نیاز بکار گیری سنگ آهن های با عیار پایین و انواع سوختهای نامناسب برای کوره بلند نیروی محرکه برای جستجو برای منابع متفاوت آهن شده است. روشهایی که آهن را با استفاده از احیای سنگ آهن در زیر نقطه ذوب آهن تولید می کند معمولاً بعنوان فرایندهای احیای مستقیم طبقه بندی می شوند و تولیدات آنها بعنوان آهن احیای مستقیم (DRI) یا آهن اسفنجی شناخته می شوند.
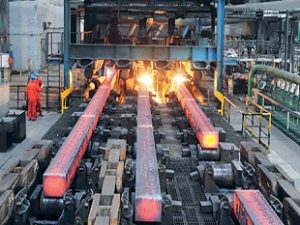
فرایندهایی که آهن مذاب تولید می کنند شبیه فلز داغ کوره بلند بعنوان فرایندهای احیای گدازی طبقه بندی می شوند. این فرایندها معمولاً به مراحل احیای حالت جامد و مراحل ذوب و سرباره حالت مایع جدا می شوند.
در سطح جهانی سنگ آهن مهمترین ماده اولیه تغذیه کوره بلندها و کوره اکسیژنی(BF-BOF) است که ۶۵/۴ درصد از تولید جهانی فولاد خام را در سال ۲۰۰۵ به خود اختصاص داده است .
اما برای استفاده از این روش باید فرآیندهای مختلفی روی مواد اولیه صورت پذیرد که نیاز به میزان بالایی سرمایه گذاری در امور زیربنایی دارد. علاوه بر این مشکلات زیاد زیست محیطی ایجاد کرده و دوره رسیدن به بهره برداری آن نیز طولانی است. در عملیات تولید کک مقدار قابل توجهی زغال به شکل کک نشو هدر می رود . با توجه به فراوانی زغال سنگ های کک نشو در مقایسه با هزینه بالا و محدودیت گاز طبیعی از این مواد به عنوان عوامل احیا کننده استفاده می شود.
برای رهایی از نواقص فرآیند BF-BOF ، روش فولادسازی EAF به وجود آمد که آن نیز عمری طولانی پیدا کرده است. سهم تولید فولادسازی قوس در تولید جهانی فولاد خام از ۲۶/۶ درصد در سال ۱۹۸۸ به ۳۳/۱ درصد در سال ۲۰۰۵ افزایش یافته است.
افزایش روند قیمت های قراضه ، نیاز بکار گیری سنگ آهن های با عیار پایین و انواع سوختهای نامناسب برای کوره بلند نیروی محرکه برای جستجو برای منابع متفاوت آهن موجب شد که به فناوری های جدیدی دست یافته و ترکیب شارژ مناسبی به صورت آهن اسفنجی( DRI یا آهن احیای مستقیم) تولید شود.
روشهایی که آهن را با استفاده از احیای سنگ آهن در زیر نقطه ذوب آهن تولید می کند معمولاً بعنوان فرایندهای احیای مستقیم طبقه بندی می شوند و تولیدات آنها بعنوان آهن مستقیم احیاء شده (DRI) یا آهن اسفنجی شناخته می شوند.
آهن اسفنجی از احیای مستقیم سنگ آهن به دست می آید که عیار آن بین ۸۴ تا ۹۵ درصد است. احیا موجب حذف یا از بین رفتن اکسیژن در سنگ آهن شده و سنگ را به صورت شانه عسل یا ساختار متخلخل اسفنجی شکلی درمی آورد که به همین دلیل بدان آهن اسفنجی می گویند.
و معمولا آن را به شکل کلوخه یا گندله ای شکل نیز تولید می کنند و علاوه بر این به صورت فشرده و بریکت شده نیز تولید می شود که بدان HBI(آهن بریکت شده گرم) می گویند که معمولا از طریق فشرده کردن DRI در درجه حرارت حدودا ۶۵۰ درجه سانتیگراد به وجود می آید. HBI شکل تغلیظ شده و فشرده DRI است که برای انبار کردن و حمل ونقل آسان طراحی شده است. DRI را می توان در کارخانه ها و واحدهای فولادسازی که در آنجا در واحدهای احیا در کنار واحد فولادسازی ها صورت می پذیرد استفاده کرد.
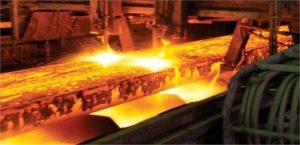
DRI در جهان یک ماده شارژ کاملا خالص و مرغوب محسوب می شود. در مقایسه با قراضه، مزایای استفاده ازHBI/DRI یکپارچگی بیشتر آن در ترکیب، عناصر مضره کمتر (به خاطر ماهیت متخلخل آن) و مشکلات کمتر زیست محیطی آن است.
ویژگی آهن اسفنجی، که در برخی از روشهای احیای مستقیم تولید می شود، عبارت است از :
۱- تخلخل زیاد به علت حذف قسمت اعظم اکسیژن کانه به وسیله اجسام احیا کننده؛
۲- ثابت ماندن شکل ظاهری گندله یا سنگ آهن خرد شده؛
۳- وزن مخصوص ظاهری کم و سطح ویژه زیاد؛
۴- عدم احیای اکسیدهای غیر آهنی و همچنین ناخالصیهای سنگ و باقی ماندن آنها در آهن اسفنجی.
امروزه روشهای احیای مستقیم، معنای گسترده تری دارند اگر توسط کربن یا گازهای حاصل از زغال و یا گاز طبیعی، احیا، ذوب یا پالایش آهن خام در حالت پلاسما انجام شود نیز جزو روشهای احیای مستقیم به شمار می آیند. در بعضی از روشهای احیای مستقیم مقداری کربن بین ۰/۵ تا ۵/۵ درصد به صورت دوده یا سمانتیت در سطح آهن اسفنجی، تشکیل می شود.